Increasing Manufacturing Efficiencies
Problem
While legacy extrusion crossheads yielded suitable product, setup was tedious and time-consuming.
Solution
Guill’s Single-Point concentricity provides quicker setups and changeovers improving manufacturing efficiencies by reducing setup time and streamlining operations.
Benefit
Reducing material waste helps reduce overall production – allowing the organization to remain competitive.
Guill Tool & Engineering Provides Mercury Wire Products, Inc. with Increased Manufacturing Efficiencies
Mercury Wire Products, Inc.
Problem - Tedious, Time Consuming Setup
For more than 50 years, Mercury Wire has designed and manufactured wire and cable solutions across a vast range of industries. With a rich history of innovation, application of lean manufacturing best practices, and a solutions-oriented culture, Mercury Wire consistently provides its customers with the highest quality custom wire and cable and integrated assemblies at the best possible value.
In its Spencer, MA facility, Mercury Wire specializes in complex constructions that begin with precise extrusion of cables using a variety of compounds including Nylon, Polypropylene (PP), Polyethylene (PE), Polyurethane (PU), and Polyvinyl Chloride (PVC). The facility leverages the latest technology in cable extrusion to produce a consistent quality product.
“Quicker setups and changeovers allow our team members to spend more time analyzing processes and activities to help reduce waste and improve the value we provide to our customers. As a result, we have improved our quality and production efficiency. Better still, we have been rewarded with greater customer satisfaction.”
Ariel Rodriguez,
Mercury Wire Products, Inc., Spencer, MA
Extrusion Expertise Is Here For You
401-828-7600
Solution - A System Designed to Deliver Quality
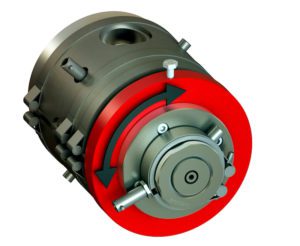
The driving force behind Mercury Wire’s Single-Point concentricity adjustment crosshead project was centered around improving manufacturing efficiencies by reducing setup time and streamlining operations. As a lean manufacturer, Mercury Wire continuously seeks opportunities to improve processes and upgrade technologies to both reduce waste and focus its resources on areas that add value for its customers. Reduction in waste in terms of both materials and time allows team members to focus more of their efforts on improving existing processes and in helping to ensure that all quality parameters are met. Reducing material waste also helps reduce overall production – allowing the organization to remain competitive. While legacy extrusion crossheads yielded suitable product, setup was tedious and time-consuming.
With Guill’s Single-Point concentricity adjustment crosshead in place, Mercury Wire has effectively realized manufacturing efficiencies supporting its mission to provide its customers with the high-quality custom wire and cable solutions they expect at the best possible value.
Benefit - Single-Point Concentricity Adjustment Crosshead
Benefits achieved using the new Single-Point concentricity adjustment crosshead from Guill Tool:
- Reduces adjustment time, directly impacting ROI
- Available on new crossheads up to 1.250” die ID
- Retrofittable to most Guill crossheads
- One bolt controls 360° of adjustment
- Standard or micro-fine adjustment screws available for precise concentricity adjustment – .008” per revolution or finer
- Fluoropolymer designs available
- Supports both pressure and sleeving applications
- Screw-off die nut compartment for easy access to die
- Easy screw-off tip retainer for access to the tip
Outcome - A Reliable System with Low Cost of Maintenance
A Reliable System with Low Cost of Maintenance
Since its installation, Mercury Wire has enjoyed continuous benefits from Guill’s Single-Point concentricity adjustment crosshead. From exploring the various options and technologies available to a fast and smooth installation, working with Guill’s team of experts was both easy and rewarding. The system has since been robust and reliable, without a single call for service. Since the installation of the first unit, several additional units have been ordered.
About Guill Extrusion Tooling
Guill Tool & Engineering is recognized as the Extrusion Technology Leader in the Design and Manufacture of Plastic Extrusion Tooling worldwide. Guill maintains the most technically capable workforce committed to the continued success of our customers by providing Quality Extrusion Tooling.
Guill Tool & Engineering also offers contract manufacturing services as well as engineering, training and consulting. All Guill products are manufactured in the USA in an ISO 9001 registered facility.